MEMoRIAL-M2.7 | Mechanical simulations of fiber-reinforced plastics based on parameters of the injection molding process
Projektleiter:
Projektbearbeiter:
M.Sc. Stefan Bergmann
Finanzierung:
Forschergruppen:

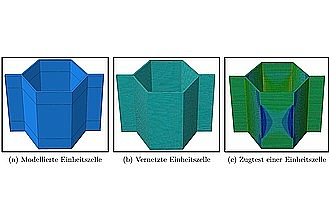
Background
In the production of thermoplastically formed honeycomb structures, simple standard material equations from various finite element method (FEM) systems fail. Differences to real experiments occur. Furthermore, each honeycomb of the structure has to be constructed, which takes a lot of time.
Objective
>> Creation of a material model that makes it possible to build the structure more simply and to still specify the stresses correctly
Methods
>> Homogenisation of the structure; spring-damper substitute model; use of a representative elementary volume (RVE); transfer of the data into a unit cell
Results
Though not for the application initially focused on, a unit cell was developed which simulates the behaviour of a honeycomb structure.
Conclusions
The work has to be extended not least with respect to a complex check for error causes in order to exclude the individually possible error sources.
Originality
A test environment was created. The determined stress values were homogenised and checked for correctness. Furthermore, the data were used in a unit cell to determine the comparison with the normal structure.
Keywords
Material model, homogenisation, honeycomb structure, polypropylene, viscoelasticity
In the production of thermoplastically formed honeycomb structures, simple standard material equations from various finite element method (FEM) systems fail. Differences to real experiments occur. Furthermore, each honeycomb of the structure has to be constructed, which takes a lot of time.
Objective
>> Creation of a material model that makes it possible to build the structure more simply and to still specify the stresses correctly
Methods
>> Homogenisation of the structure; spring-damper substitute model; use of a representative elementary volume (RVE); transfer of the data into a unit cell
Results
Though not for the application initially focused on, a unit cell was developed which simulates the behaviour of a honeycomb structure.
Conclusions
The work has to be extended not least with respect to a complex check for error causes in order to exclude the individually possible error sources.
Originality
A test environment was created. The determined stress values were homogenised and checked for correctness. Furthermore, the data were used in a unit cell to determine the comparison with the normal structure.
Keywords
Material model, homogenisation, honeycomb structure, polypropylene, viscoelasticity
Anmerkungen
Wiss. Co-Betreuende / Scientific Co-Supervisors: Dr.-Ing. Matthias Zscheyge (Fraunhofer-IMWS, Halle/Saale)
Kooperationen im Projekt
- Fraunhofer-Pilotanlagenzentrum für Polymersynthese und -verarbeitung PAZ, AG Thermoplastbasierte Faserverbund-Bauteile, Schkopau, GER
- Fraunhofer-Institut für Mikrostruktur von Werkstoffen und Systemen IMWS, Halle/Saale, GER
- Dr.-Ing. Matthias Zscheyge (Fraunhofer-Institut für Mikrostruktur von Werkstoffen und Systemen IMWS, Halle/Saale)
Publikationen
Die Daten werden geladen ...
Kontakt

Prof. Dr.-Ing. habil. Dr. h.c. Holm Altenbach
Otto-von-Guericke-Universität Magdeburg
Institut für Werkstoffe, Technologien und Mechanik
Universitätsplatz 2
39106
Magdeburg
Tel.:+49 391 6758814
weitere Projekte
Die Daten werden geladen ...